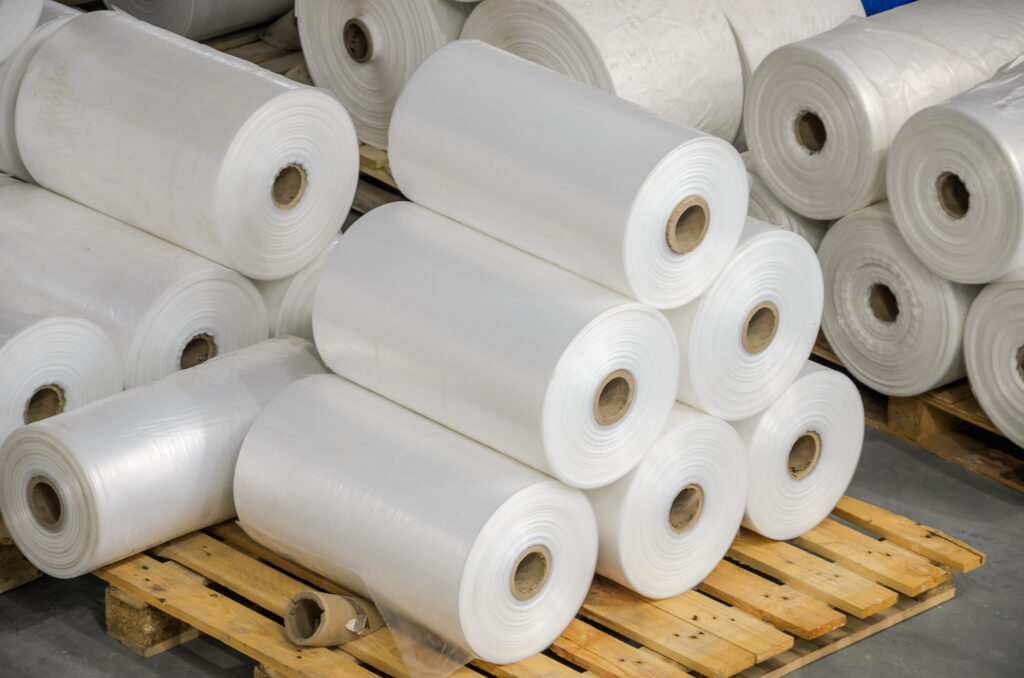
If you’ve received a t-shirt or other soft goods in the mail, there’s a very good chance it came in a soft package that was sized to fit the item – and most likely in the shape of a square or rectangle. For this application, the film needs to conceal the product within, be flexible, and have high resistance to puncture, tearing, and abrasion to survive the shipping channel.
Other products or applications need a film that creates a more rigid wrap that can, for example, hold more than one item together. Just go into your local superstore and find the peanut butter aisle. Most often, there are two jars of peanut butter solidly joined together to form one package. This is what we would call a heavy multi-pack. To keep these items bound tightly together, a film with a high modulus or stiffness is needed.
The best way to identify the proper film for the job starts with identifying the object. Does the item need to be tightly contained? Is it a unique shape that needs a shrinkable film? Will it be used for tamper resistance/evidence? Does it need high clarity to see the product? Will the product be wrapped at a very high rate of speed? Can the product be easily crushed or curled? Is it a larger item that will be handled by consumers?
For example, a case of water bottles is heavy and has numerous loose bottles (another multi-pack.) this requires a film with a lot of shrink force to help keep the loose bottles tightly bundled together. A bonus to this bundled package is the bullseye seals on the sides that become built-in carry handles. This film must also be soft to conform tightly to the package and offer low puncture resistance as Most consumers open these packages by pushing their finger through the film between the bottles. If this were a stronger film, that wouldn’t be as easy to do.
Two popular film options that wrap a variety of items like those mentioned above, are polyolefin and polyethylene. Understanding their capabilities and application uses, will determine which one is needed for the job.
Polyolefin, the film used to wrap the peanut butter jars, is a high clarity film available with many options for performance characteristics. It is well suited for most retail applications. For example, this film can be shrunk to fit around an object with a unique shape – such as a heart-shaped box of chocolates, or gently hold a package of hard taco shells, and can tightly wrap around a product like bug spray to ensure that it is safely contained. It can also be used for medical applications, where an item is completely enclosed providing a sterile package. Polyolefins are typically available in thicknesses from 200 gauge (2mil) down to 30 gauge (0.3mil.)
Polyethylene, the film that is used to wrap a case of water bottles, has a thickness that ranges from about 0.8mil up to 7 or 8 mil, but is typically used between 2-4 mil in most applications. It is usually about one quarter the price of polyolefin pound for pound. Because of this film’s characteristics it is generally used in thicker gauges. This can sometimes offset the price advantage over the thinner polyolefins.
To choose the right film, first identify the product – understand its application and how it will ship and be handled. Once you determine that, choosing the right film should be a straightforward decision. Machines such as the Kayat 801/802-TGS Shrink Wrapper can then use these films for shrink wrapping in a variety of industry applications.
Brian Dennis is the Southeast Regional Sales Manager for Texwrap. He can be reached at brian.dennis@promachbuilt.com; https://www.texwrap.com/.