Would you rather have a shrink-wrapping machine that stops and starts for each seal cycle or one that only stops when it’s time to change products or a roll of film? Otherwise known as intermittent and continuous motion sealers, respectively, choosing the right option between these two wrapping styles can set you up for success. While the intermittent model stops the belt to allow each product adequate time at a stationary seal bar, the continuous motion machine uses a traveling seal bar that goes with the product during the seal cycle to maintain that all-important seal dwell time.
Much like how city or highway driving can influence the speed and smoothness of a drive, intermittent or continuous motion can have a major impact on the same factors in a packaging line. Answering the question of which to choose requires a breakdown of the cost, expected speed, and product stability for indications of how each would impact your operation.
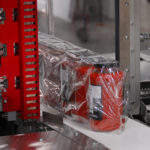
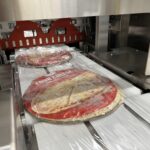
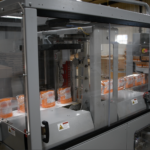
Cost
Choosing continuous over intermittent motion may seem like the obvious option, but for smaller operations that are taking their first step into automation, intermittent may be the way to go. Intermittent machines have a much lower upfront cost than the more robust continuous models. If the required throughput and products are compatible with intermittent motion, going with the more cost-effective choice is the logical conclusion.
Expected Speed
One of the main reasons to go with the continuous system is
a line’s required throughput. Intermittent motion sealers typically run between
eight and 25 packages per minute. A small package like a CD case can run
faster, but high-speed stopping and starting can cause undue wear and tear on
the machine. On the other hand, for consistent high-volume applications, continuous
motion machines can run at speeds producing 100 packages per minute or more.
Manufacturers looking to add one of these machines should also keep in mind future growth. If the line is already running on the higher end of an intermittent machine’s capabilities, proactively opting for the continuous model can help ensure longevity.
Product Stability
Regardless of the machine’s speed, some products are simply not suited for intermittent motion. For lighter objects such as sheets of paper, the constant stopping and starting can cause shingling and shifting that disrupts the shape of the stack. This can lead to excessive film use, rejections, and even damaged products. Heavier items can also be impacted if the base is small. For example, 50ml bottles of alcohol (airplane bottles) and wine bottles can topple over as the machine stops and starts for every cycle.
Continuous motion’s smooth conveyor movement is more harmonious, and products do not fall or shift out of position. If the product going through the line may be vulnerable to these issues, continuous motion is the right call, no matter the throughput speed.
Both options have features that make them better for some operations than others. To learn more about whether you would be more successful with an intermittent or continuous motion sealer, talk to your sales representative today.
Brian Dennis is the Southeast Regional Sales Manager for Texwrap (www.texwrap.com). He can be reached at brian.dennis@promachbuilt.com.